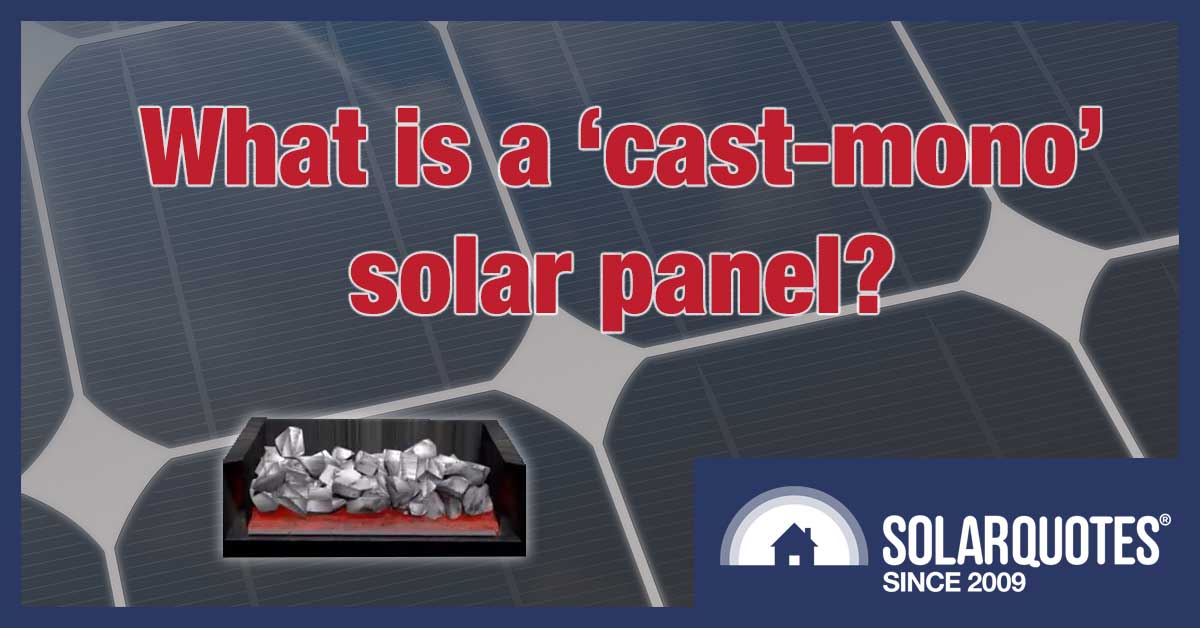
You’ve probably heard of mono and poly panels. Now there’s a third type: ‘cast-mono’. But what the hell is it?
Silicon is the Queen of solar power. Some people say Coal is King, but I say our Queen can kick your King’s arse. Only 5 years ago thin film cadmium telluride1 panels were still being installed on home roofs, but they have disappeared from the residential market leaving silicon to rule the roost with an iron beak.2
While Silicon is Queen, not all silicon is the same. There were two big silicon princesses3 that have been battling for market share. Polysilicon is quick and cheap while monosilicon is more expensive but also more efficient.4 But now there is a new contender that’s made in a container — cast monosilicon!
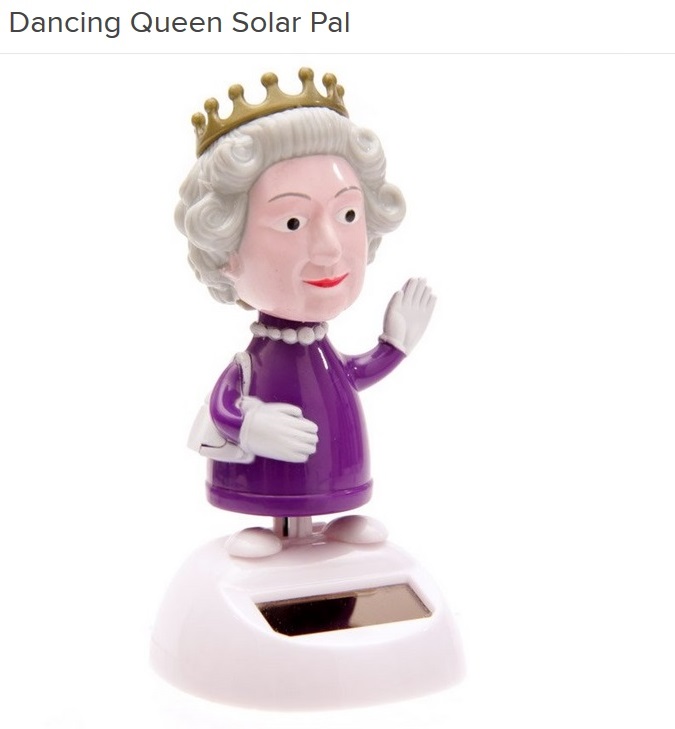
ABBA: She was the Solar Queen, Regal and sweet, Only ninety-three…
Cast monosilicon5 – or cast monocrystalline silicon if you’re being paid by the word — has been around for years but didn’t make a splash6 until recently when the process was improved. It is now almost — but not quite — as efficient as monosilicon, while being almost — but not quite — as cheap as polysilicon. It has the advantage of lower LID, which is a type of solar cell degradation, and the less there is of that the better.
There are at least 9 manufacturers currently making panels with cast monosilicon solar cells. These include two big ‘uns:
- Canadian Solar, and…
- GCL
GCL got the ball rolling on cast monosilicon back when they were solely a silicon producer, so it’s not surprising they’re using it for panels now.
But while cast monosilicon may become popular, at the moment it doesn’t have the power to get rid of polysilicon. This is because the current process creates both cast monosilicon and polysilicon at the same time.
Mo’ Crystals, Less Efficiency
If you promised your girlfriend/boyfriend/roboprostitute a big diamond ring but then handed over one with a gemstone made of hundreds of tiny diamonds glued together, you’d soon find yourself sleeping on the couch/in the doghouse/in a bioslave reprocessing vat.
The moral of this real life example is simple. When it comes to diamonds, one large crystal is better than many small ones. The same is true for silicon and solar cells:
- Polysilicon Solar Cells = Many silicon crystals and lower efficiency.
- Monosilicon Solar Cells = Made from a single large silicon crystal and higher efficiency.
Monosilicon cells are roughly 5% more efficient than polysilicon ones, which is enough to boost the efficiency of a solar panel by around one percentage point. So if all else was equal and you changed a panel’s cells from polysilicon to monosilicon, its efficiency might go from 18% to 19%.
Making Poly (Without A Mummy And Daddy Parrot)
Monosilicon is more efficient for complex sciency reasons that I fully and deeply understand at a very profound level — but which I won’t go into because I don’t want to bore you with the details. What’s important is less efficient polysilicon is cheaper to make because:
- The energy required costs less.
- The equipment required is simpler, so capital costs are less.
To make polysilicon high purity silicon is melted and allowed to cool in a molds. As the temperature falls multiple crystals are formed. The slower it cools the more time the crystals have to form and the larger they’ll be. For example, steel crystals are normally very small, but when slowly cooled in the heart of a baby planet like this meteorite, they can be quite large:
Large crystals of nickle-iron stainless steel in a meteorite. (Image: Wustledu)
Silicon forms much larger crystals and so they don’t have to spend an eon slowly cooling in space7 to be easily visible, as this photo of a polysilicon solar cell being held by an alien shows:
After the polysilicon has cooled it is taken out of the molds and then cut into blocks. These blocks are then cut into thin wafers to make solar cells with little waste because the original ingot was in a convenient shape to make square solar cells.
Making Mono
Monosilicon costs more to make because it requires a lot of control. High purity silicon is dumped in a big round quartz pot and melted. (Quartz is one of the few things that doesn’t melt before silicon does.) The pot is heated with electricity so its temperature can be perfectly controlled. But electric heat is more expensive than heat from burning natural gas used for polysilicon and this is one reason why monosilicon costs more.
When the liquid silicon is ready, a rod with a silicon crystal seed is dipped in. This is important because, at the right temperature, the atoms in liquids can be ready to get crystallized but can’t be bothered to do anything until an example is set for them by an existing crystal and then they begin to fall into line.8 Here’s a video clip with super cool water being shown how to crystallize by an ice cube on a tray:
After the seed crystal is dipped in the molten silicon it is very slowly extracted. At the same time the rod it is attached to and the pot it’s in are very slowly rotated in opposite directions, allowing a large, single crystal ingot to be drawn out. Here’s a video with a super terse narrator on how it’s done:
Finn — my boss — used to write software that controls machines that make ingots this way, except they were sapphire instead of silicon.9 This method is called the unpronounceable process. It does have a proper name, but before I relay it you have to promise you won’t blame me for any tongue injuries that may result. It’s called the Czochralski process.10
It can take two days to make a monosilicon ingot this way, so a lot of these devices are required for high output. There’s also a lot of waste because the edges of the round ingot have to be cut off to make square solar cells. But despite having drawbacks, monosilicon’s higher efficiency gave it the edge it needed to take market share away from cheaper polysilicon until the two were neck and neck. Monosilicon’s eventual dominance seemed assured, but now cast monosilicon has arrived on the scene and wants its time in the sun.
Back in ye olden days — such as 1972 when this panel was made — silicon was a lot more expensive, so they made round solar cells to prevent waste.
Making Cast Monosilicon
Cast monosilicon is cast from a mold similar to polysilicon, but monosilicon wafers are placed at the bottom to act as seeds for crystal formation. This video shows an animation of how it’s done:
After watching it I don’t understand what stops the seed silicon from melting. My guess is the process is more complicated than it seems.
In the animation the ingot of silicon appears to be large enough to be cut into 24 blocks and each of those blocks will be cut into wafers to make solar cells. But only the 8 blocks from the centre will be cast monosilicon.
Because the silicon near the edges of the mold cools more rapidly it contains multiple crystals and will be somewhere between standard polysilicon and cast monosilicon. If the entire mold was cooled more slowly it could give enough time for all the silicon to form one large crystal, but this may be impossible in practice because contaminants — especially oxygen — can diffuse into the silicon from the mold walls.
Cast Monosilicon Has Defects
Cast monosilicon doesn’t create almost perfect crystals like standard monosilicon production. When monosilicon is slowly pulled out of its quartz pot it relieves pressure created by the silicon contracting as it cools, but because this can’t happen in a cast monosilicon mold it results in defects. These can be seen with the naked eye, but aren’t nearly as obvious as the multiple crystals in polysilicon. These defects reduce the efficiency of cast monosilicon but, when done right, still gives a considerable improvement over polysilicon.
An ingot of cast monosilicon. Note it’s not really that big. This is forced perspective, like when someone puts a gun against your head and says, “Can’t you see things from my point of view?” (Image: PV-Manufacturing.org)
You may be concerned when you buy a cast monosilicon solar panel that instead of getting the good stuff from the centre of an ingot, you’ll get the lower efficiency polysilicon from around the edges. While it has more visible defects it can still look much the same as cast monosilicon, and someone who isn’t familiar with solar panels can’t be expected to tell the difference.
The good new is manufacturers aren’t allowed to lie about the performance of their panels. If they claim a panel is 300 watts then it has to be 300 watts no matter what. They can’t just substitute lower quality silicon that will only give 290 or 295 watts. So provided you avoid crap solar and buy from a reputable manufacturer you should be fine.
Lower LID
LID stands for Light Induced Degradation – it occurs to solar panels during their first couple of days in the sun and typically reduces panel efficiency by a couple of percent. This is enough to reduce a 19% efficient panel down to 18.6%. Cast monosilicon suffers from less of this. This is a good thing, but don’t get too excited because even if LID is cut in half the advantage will only be small. But even a small advantage is a good thing to have.
Cast monosilicon’s lower LID results from its lower oxygen content. Less oxygen in silicon is mostly good, but one drawback is it can make solar cells more brittle and result in more breakage during manufacturing.
Cast Monosilicon’s Future Looks Sunny
Because cast monosilicon can give close to monosilicon efficiency at close to polysilicon prices, its popularity seems assured and a whole slew of manufacturers are likely to use it. Possibly even a huge slew. If we divide the world up into different manufacturing regions there could even be a few huge slew. If you are offered cast monosilicon panels from a reputable manufacturer I don’t know of any good reason at this time not to use them.
Footnotes
- Cadmium = toxic. Telluride = toxic. Cadmium telluride = non-toxic. It’s a bit like table salt. Two dangerous elements combine to make something you can eat. Note: Don’t eat cadmium telluride. ↩
- Or since silicon is a semi-metal, probably not an iron beak at all. ↩
- Yes, they are Princesses of Power. ↩
- Kind of like the difference between a Dutch and a German lover. ↩
- Cast monosilicon is also called casted monosilicon. Probably because some foreign people don’t realize how much the English language sucks when it comes to irregular verbs. ↩
- Warning: Do not splash in molten silicon. ↩
- We’re talking about a cooling rate of a few degrees over a million years here. ↩
- Or not a line at all, but a three dimensional lattice. ↩
- Finn is all about the bling. ↩
- Jan Czochralski discovered it after dipping his pen in the wrong pot. A Prussian German living in Poland, he worked for the resistance during World War 2. For his trouble, he was accused by the Soviets of collaborating with the Nazis. ↩
Thanks for the overview, so 9 comanies work with it! Good!
I mighr read it badly, but the point is no waste from sawing and overall simpler according to the reference below
https://www.pv-magazine.com/2019/02/26/1366-technologies-and-hanwha-q-cells-to-open-wafer-factory-in-malaysia/
Great tech article Ronald…
Here’s some edits…
1) The the moral of this real
2) So if if
3) it occurs to solar panels ==> it occurs on solar panels
4) there could even be a few huge slew ==> there could even be a few huge slews
Thank you for correcting my my stutter. But I am leaving slew as it is because I have the power to create one new word a day. I know some people don’t yabalish this when I tell them, but it’s true.
crystal seed has molecules arranged in a grid so that molecules have stronger bonds between each other than in amorphous form.
for this reason crystal seed does not melt at melting point of amorphous form.
Thank you for that information, Sergey.