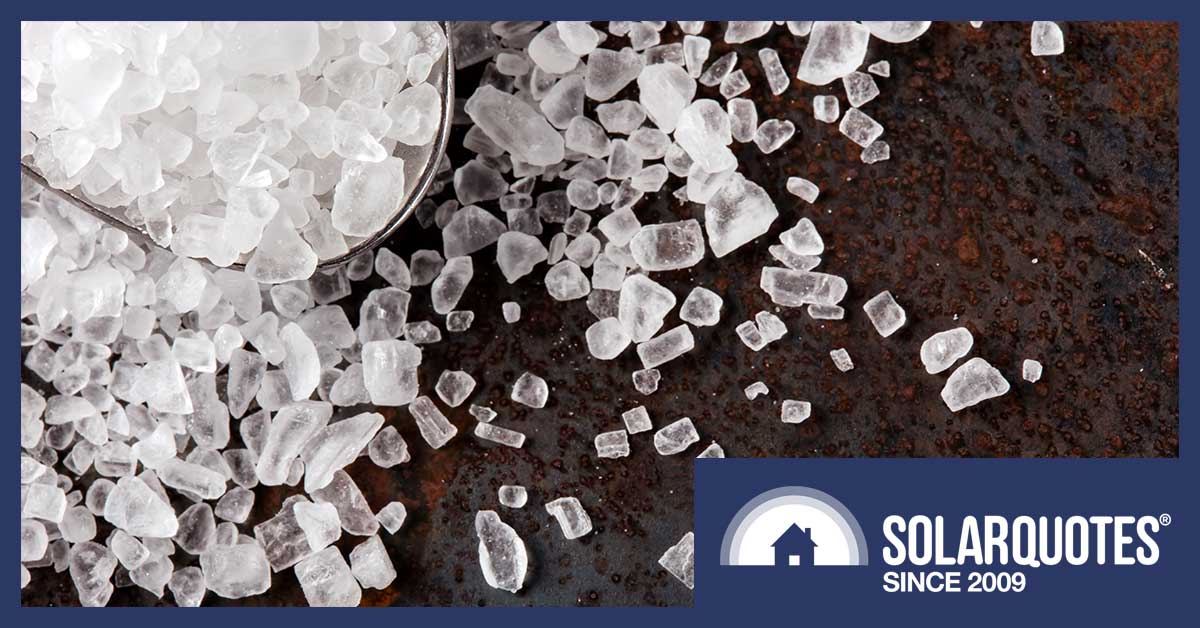
Table salt could hold the key to bigger, cheaper Li-ion batteries.
Just before Australia went into its traditional summer stupor, someone from the Pacific Northwest National Laboratory (PNNL) in America got in touch with me about research into single-crystal technologies for Lithium-ion batteries.
The twin challenges of Li-ion batteries are to improve their energy performance while making them cheaper, and that’s behind PNNL’s materials science. The focus of this project (published in Science Magazine here) is to overcome the problems involved in making nickel-rich single-crystal cathode components. As the PNNL press release explains, increasing the nickel in a cathode lets a battery store more energy, but too much nickel and you get an unstable cathode.
The other focus of the PNNL work is to overcome the problem of the cracking that polycrystal cathodes can suffer, since those cracks shorten battery life.
From PNNL’s media statement:
“Currently the most common nickel-rich cathode is in the form of polycrystals – aggregates of many nanocrystals in one larger particle. These carry advantages for storing and discharging energy faster. But the polycrystals sometimes break down during repeated cycling. This can leave much of the surface area exposed to electrolyte, accelerating unwanted chemical reactions induced by high nickel content and generating gas. This irreversible damage results in a battery with a nickel-rich cathode that fails faster and raises safety concerns.”
That problem is worse when a crystal is rich in nickel, because nickel can introduce unwanted chemical reactions, PNNL said.
Cathodes made out of nickel-rich monocrystals should avoid that particular challenge, but monocrystals suffer their own degradation problems, as PNNL battery group team leader (and corresponding author of the Science paper) Jie Xiao explained to me in December.
The first issue is fabrication.
“To grow single crystals, you need a higher temperature, and that means lower performance”.
“Lithium salts evaporate at high temperature – the longer you hold the crystal at a high temperature, the more lithium you lose. That will lead to lower capacity.
“Another thing – because we’re talking about nickel-rich crystals, at high temperature, you don’t get the ideal structure. You will get nickel oxide.”
Xiao’s team at PNNL decided to take a different approach to fabricating the monocrystals.
“We used sodium chloride – table salt – as the ration medium to allow the crystal to grow,” Xiao explained. “That helps lower the temperature, and reduce the [crystal growth] time.”
The other important discovery the team made relates to what causes a monocrystal to break down, a process they described as “crystal gliding”.
Xiao again:
“What we found is that the single crystal – they do not break down into small pieces. Instead the layers of the structure are gliding towards each other.”
This is illustrated in the following animation:
What’s encouraging is that through the group’s new-found understanding of the process, they also found it can be alleviated with relatively simple measures.
Gliding, Xiao told me, is reversible, and only causes irreversible damage after either extensive cycling, or charging to very high voltages.
Cycling is just life for a battery, but battery charge voltage is easy to manage. Limiting the per-cell voltage to 4.2V helps prevent gliding, Xiao told me – and that’s the normal charge window for Li-ion batteries.
Crystal structure is the other way to manage gliding, Xiao explained. 3.5 microns turns out to be a critical crystal size, at which gliding is mitigated or eliminated; and modifying the monocrystal’s symmetry also helped.
The payoff of this work? The PNNL team estimates that a single crystal nickel-rich cathode holds 25% more energy compared to the Li-ion batteries currently used in EVs.
Xiao said further work will focus on scaling up their fabrication techniques, using other discoveries to be published in the future to replace the sodium chloride growth medium.
Speak Your Mind